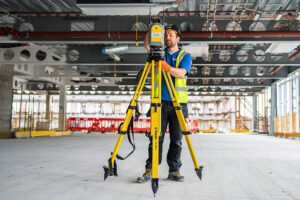
Download a formatted PDF of the story here
- Stand out benefits for Derry Building Services and Bell Ventilation:
- Reduction in working at height (110 days)
- 400% increase in productivity for setting out FCUs
- Ease of use and straight forward adoption of the new workflow
- Reduction in errors associated with manual measurement methods
- Excellent level of support from BuildingPoint UK & Ireland
How Derry Building Services and sub-contractor Bell Ventilation were able to decrease the setting-out time of 996 fan coil units by over 400% using a Trimble Ri digital layout solution and FieldPoints software, all supplied by Trimble BuildingPoint UK and Ireland.
Pilgrim’s Quarter, part of the Pilgrim Street development, is a new office development in the heart of Newcastle City Centre. The £155m project will see the regeneration of the northern block of Pilgrim Street which will include the retention of the historic facade of the art deco Carliol House in preparation for it becoming the largest of HMRC’s 14 regional centres and home to 9000 workers.
Responsible for the setting out and installation of the fan coil units on this project is Bell Ventilation Services, a family run company specialising in the design, manufacture, and installation of ventilation solutions. Operating out of its manufacturing facility in Blyth, Northumberland, Bell Ventilation is serving an ever-growing customer base and establishing itself as a company capable of successfully delivering large scale projects.
The company is therefore actively exploring technology to enhance its service as well as new ways to implement work practices that will significantly boost productivity, particularly on larger sites such as the Pilgrim’s Quarter project which required the set-out and installation of 996 fan coil units across 11 floor plates.
Elevating workflow efficiency
Before the ventilation contract was awarded to Bell Ventilation, Company Director Martin Bell worked closely with DBS’s Mechanical Project Manager, Steve Mann, to see how the existing manual workflow for fan coil unit setting out could be digitised through the introduction of digital layout technology.
Already familiar with Trimble’s Ri and Field Points software ( which ensures points in the model are accurately located in the field), Steve Mann contacted BuildingPoint UK and Ireland to arrange a trial of the system for Martin to take a look at.
The existing workflow saw the Bell team working from paper plans with gridline offsets. On site, manual measurements were then taken from the soffit which meant platforms were required for working at height. Taking the measurements required two people and although the job was not complicated it was extremely time consuming. The manual process was also subject to potential errors due to these methods.
Although Martin was initially concerned that the Trimble Ri system might be technically complicated, the trial alleviated these concerns and both Steve and Martin felt that its introduction was ‘a no brainer’ for the project.
New workflow
In the office: The Revit model is prepared by Derry Building Services and includes all the fan coil locations. Using an automated process and a ‘place points over markers’ function, the Trimble Field Points software generates accurate setting out positions for all the required points where the fan coil will be fixed. The automated feature easily applies the accurate positions to all points, even those on fan coils that are not of a standard size. On this project, over 3,900 attachment points were generated.
The job is then exported into Trimble FieldLink software on a tablet for use on site in conjunction with the Trimble Ri.
On site: The Bell Ventilation field team opens up the model on the tablet and selects the floor plate they are working on. They can then see where the fan coil units are to be located along with the ducting, vents and attachment points. The software connects to the Ri and one of the Bell team sets up its position relative to the gridlines. The first point is then tapped on the tablet and the Ri’s laser points to the corresponding position on the slab. A vertical laser is then used to locate this point on the ceiling.
As each point is stored, the software checks that it is within tolerance, in this case within 50 mm although the Ri is capable of delivering mm accuracy. A revision cloud can then highlight anything out of tolerance for further action when the file is imported back into Revit. A report is also generated for each fan coil unit to show that it has been accurately installed.
The Bell team now comprises of one member marking the fixing points (this was previously a two man job) followed by a team of two installing the units.
Crunching the numbers
The system’s primary objective was to enhance site health and safety by minimising work at heights. Additionally, it aimed to ensure commercial viability, boost productivity, and optimise labour allocation for Bell. Consequently, the meticulous monitoring of site work results was crucial for both Steve and Martin, ensuring that the financial metrics aligned with the intended goals.
- 996 fan coils to be fitted over 11 floor plates.
- Over 3900 attachment points generated.
- Each floor requires either 3 or 4 set ups of the Ri with each set up taking less than 30
- Using traditional set out methods (paper plans and tape measurements) the Bell team completed the marking up and fitting of 8 fan coils a day. Using the new Trimble system for setting out they completed 20 units in a day. The setting out process on its own was 400% faster than previously and saw a single team member set out 640 points a day compared to around 32 previously.
- A job that would have taken 116 days to mark out manually could now be undertaken with the new Trimble Ri workflow in just 6 days.
- 110 days saved working at height.
Far reaching benefits
Although initially concerned about how easy the system would be to use, Martin reports that his team had no trouble in quickly adapting to the new workflow with one team member using the Ri productively in just 2 hours: “Initially, we were concerned about any technical issues the new workflow may present and how long it would take to get the team trained up but that simply wasn’t the case. The team took to it well and we now have a far better flow on site with just one of the team marking the fixings and two following for the installation. Marking out 20 units an hour means there’s never any hold up.”
Steve Mann concludes: “I’ve known about the Trimble Ri technology for some time following a recommendation from a friend. This project has circa 1000 FCU and the shape of the building and complex steel work would have made traditional mark up near on impossible. The biggest loss on a job is down to overspend on labour, I wanted to use this system to reduce working at height and at the same time, speed the install up.
“Moving forward, we’re looking at utilising this technology throughout Derry Building Services. In my opinion, the system has over delivered and I’m looking forward to implementing it on future projects.”
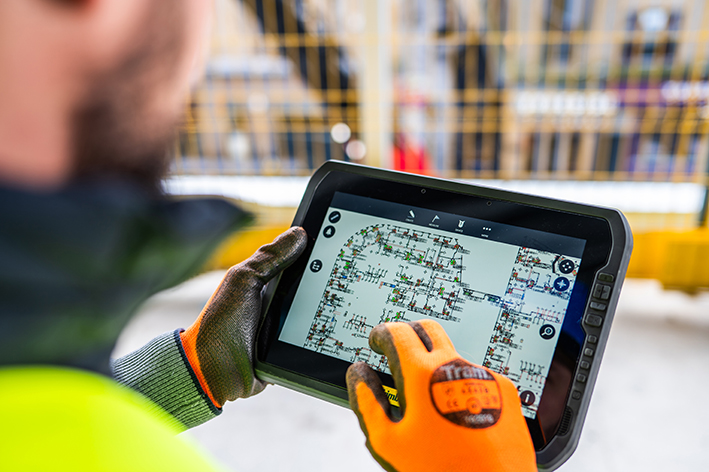
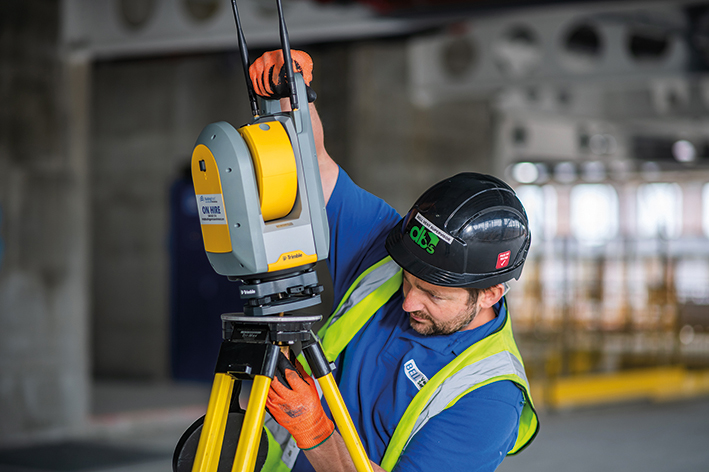
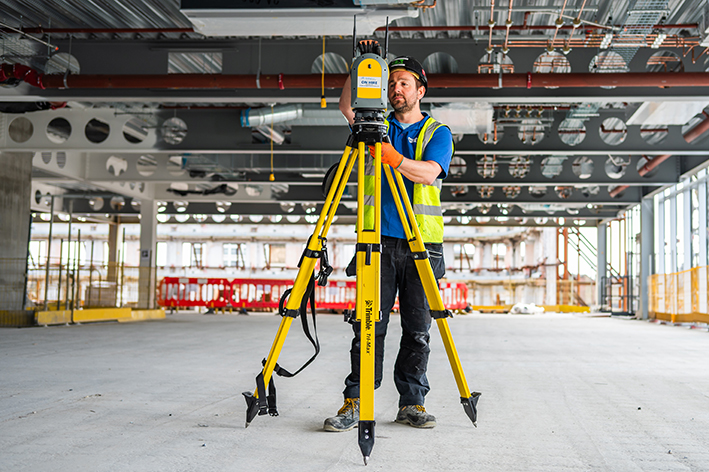
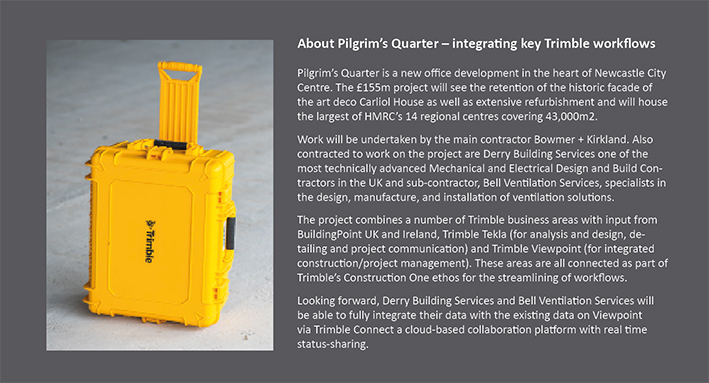